Making of Himalayan Village Sonapani
As I bid my final goodbye, I fondly remember an association of over one and a half decade with a venture which, in terms of scale and involvement, was one of the most challenging, exciting and fulfilling project for me.
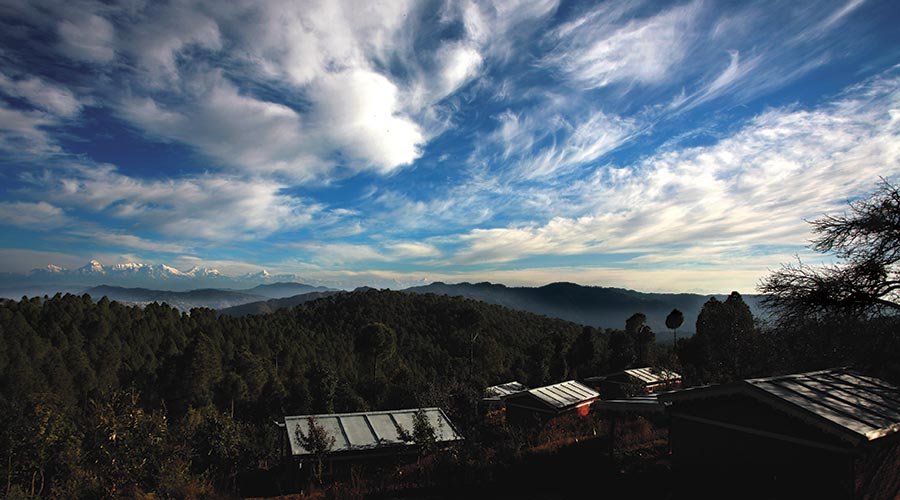
The journey started rather strangely. I was exploring options to move back to Uttarakhand and accidently bumped onto a school mate who wanted to do something in hospitality sector. I had met the schoolmate after decades through a colleague who happened to tell me that she had friends who hailed from Haldwani, my hometown then.
We had dreams but no money hence instead of buying land we searched for land on lease. It took us well over a year to finalize the location. Funnily my partner had initially rejected the land which we finally settled for. When we were left with no option, he suggested that I see the land which he had seen a year ago but did not like. The moment I saw Sonapani estate, I fell in love with the possibilities. It was precisely the terrain and landscape I was looking for.
It is a great plus to be a designer when one is penniless. Literally all aspects of design fell on my lap – right from working out lease and partnership contracts to evolving the concept and vision, brand name and identity, business design & strategy, land development, architectural design, landscaping, furniture design, website, brochure, posters, presentations, and so on. Not outsourcing any aspect of work helped curtail costs and streamline available resources. It took us one and half years to setup the place. There were many hurdles on the way – right from funds to logistics to people management to partnerships… but we emerged fine and created something which numerous visitors fell in love with.
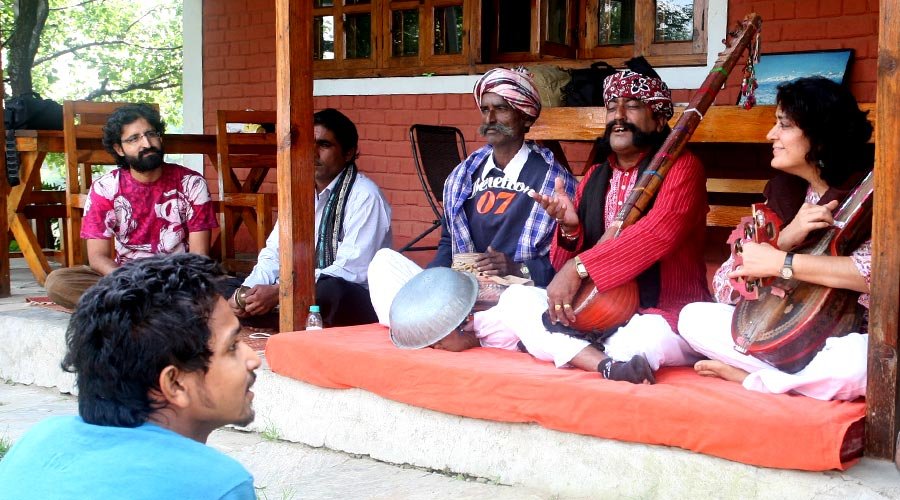
The overall business plan was not limited to hospitality. We leased 20 acres of land so that we could also engage in organic farming and handicrafts to subsequently integrate with local ecosystems – becoming a channel for outflow of goods and inflow of essential services. The overall business plan was to extend the venture to closely partner with at least 100 villages within a decade. Due to some partnership issues these aspects of business could not take wings.
The land we took on lease was a barren estate with a 100 year old house seeking repair. There were rats on the roof and snakes on the wall. The location was 1.25kms walk from the road. There was no phone connectivity. No wonder many were laughing at our misadventure.
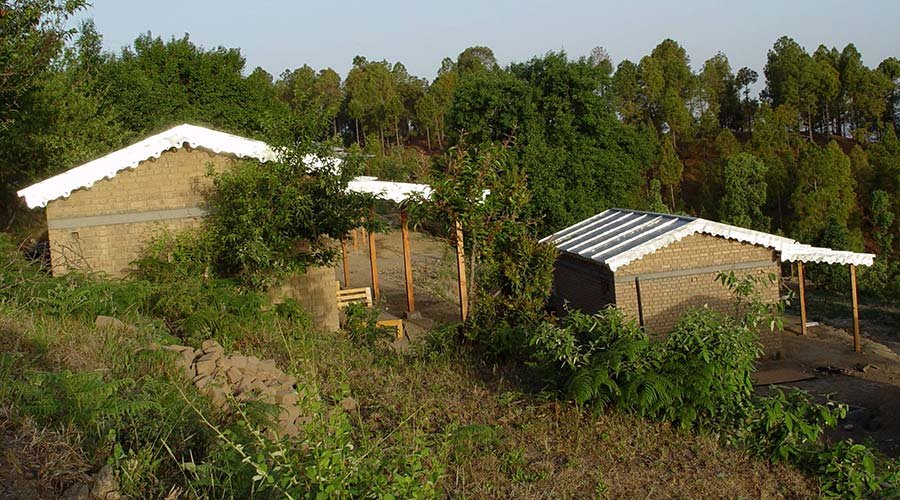
To curtail the cost and make something eco-friendly we opted for alternative building technologies. A dear friend, Harsh Kakkar, came to our rescue. He not only suggested various options but also helped us find organizations that could help us with machinery and training. Thanks to him, we could afford separate septic tanks for every cottage at exceptionally low cost, using a second hand bitumen drum, few stones and a locally fabricated concrete lid.
We choose to construct the entire setup using compressed mud blocks. As we had to dig the land for laying the foundations, we used a large part of that soil for making mud bricks. We used Tara Balram machine from Development Alternatives to make over 100,000 sun baked compressed mud blocks. A trainer from DA trained our team to use this manual machine efficiently. Within a matter of days we were clocking well over 1000 bricks per day. 14 days of sun baking and the bricks were ready to be laid.
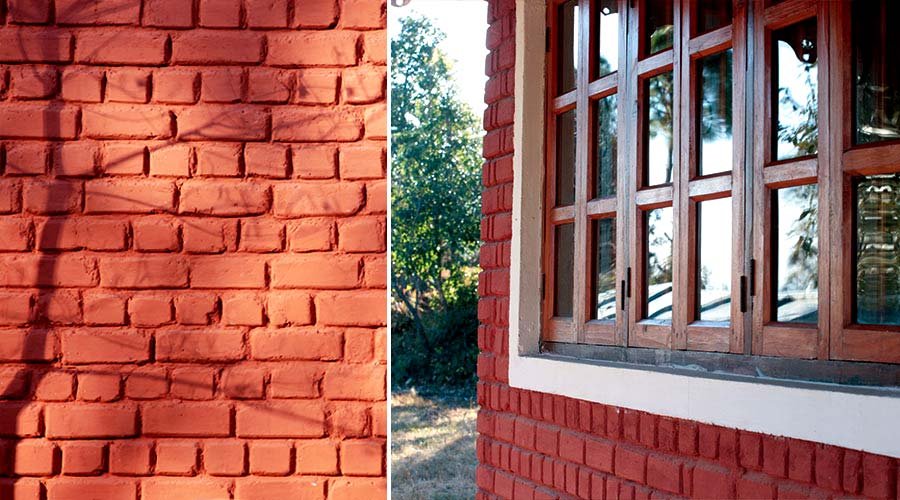
Use of mud blocks not only reduced the cost of basic building block but also saved a lot of money as we used mud mortar to lay the bricks and room interiors were mud plastered. The mud plaster was made using local mud and mule dung. The plaster so created not only gave a good finish but also turned out to be very stable and long lasting. The external surface was left exposed but we soon realized that incessant rains were damaging the infrastructure so opted for weather coating the exteriors. The mud blocks not only minimized our environmental footprints but also generated local employment.
As per the advice of Harsh, we constructed concrete rings at plinth level to tie the structure together for enhanced earthquake resistance. Many people doubted if the structure will survive the impact of weather and time. Well, they are standing tall for well over 15 years now and show no signs of breaking down.
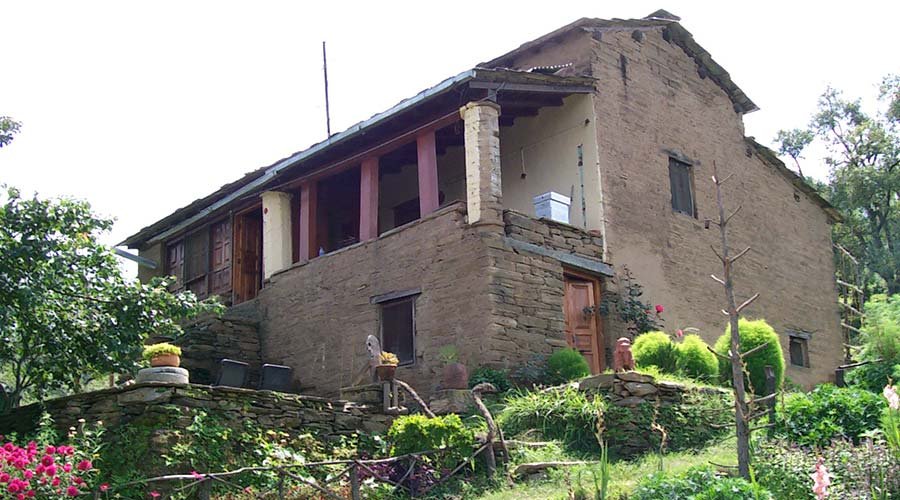
The 100 year old stone house was repaired. The first floor served as our corporate headquarters whereas the ground floor became our staff quarters and store. Adjacent to this house we constructed a modern kitchen which was made accessible to our guests. Numerous guests have used the kitchen. And many of them passed on unique skills to the kitchen staff.
We did not want to waste money on land development. We also did not want to disturb the terrain hence the cottages were laid out as per the existing topography of the land. Such an approach not only helped us integrate the cottages well with the landscape but also gave a very organic village-like feel to the place, justifying the brand name – Himalayan Village.
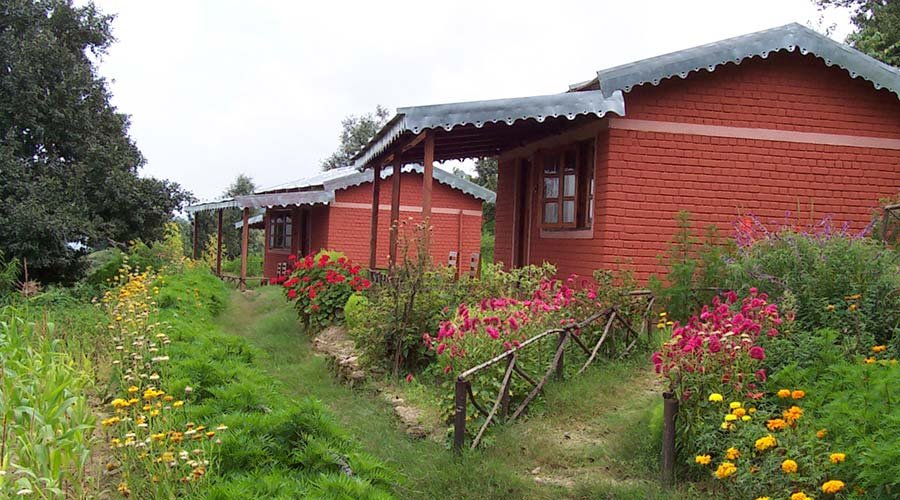
We built 10 regular cottages (19 feet by 11 feet) and two family cottages. The family cottages have an extra enclosure (not doored) with a bunk bed for children. The large windows (8 feet by 4 feet) on the front side provided good air circulation and a wonderful view of the Himalayan range. For those who ignore the signs of climate change, it is worth mentioning here that we discussed at length to optimize the size of the window so that the cottages do not get very cold during non-summer seasons. Within a decade we had guests who blamed the architect, which means me, for making a room sans circulation and providing very small windows. We never provisioned for fans. The mud bricks structure meant that we did not need heaters. Within a decade the guests were demanding fans. Higher influx of guests during winter months brought in the room heaters.
Every cottage at Himalayan Village Sonapani has a covered sitting area in front from where one can endlessly gaze the almost 180 degree view of the majestic Himalayan ranges with Mount Trishul and Nandadevi peaks hogging the limelight.
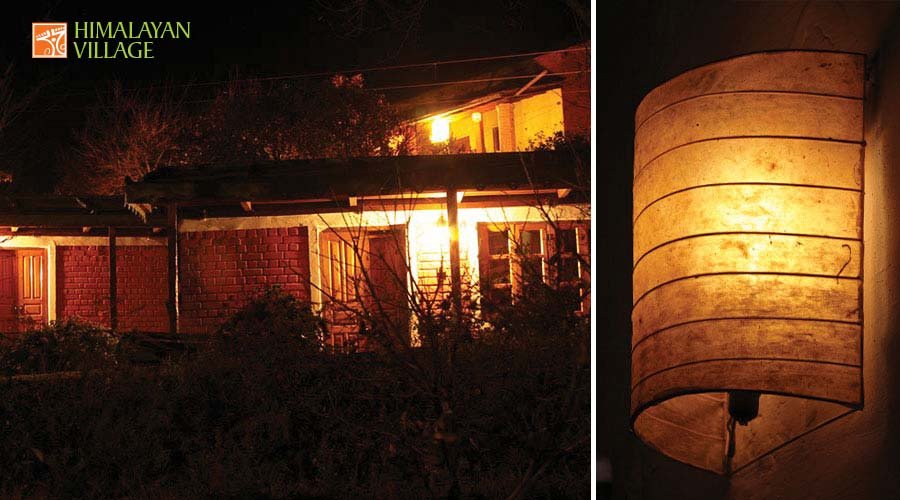
We also engaged in a massive woodworking exercise. Every piece of furniture was designed and fabricated locally, that included the table lamps. We got the lighting fixtures fabricated at Gurgaon as gas welding options were not available at Sonapani. The welded metal frame was clothed with handmade oil paper. Please do not confuse these designs with fabindia products as we designed and fabricated these pieces much before fabindia started selling them. The dining hall furniture was designed in a way that we could quickly convert the restaurant into a conference hall.
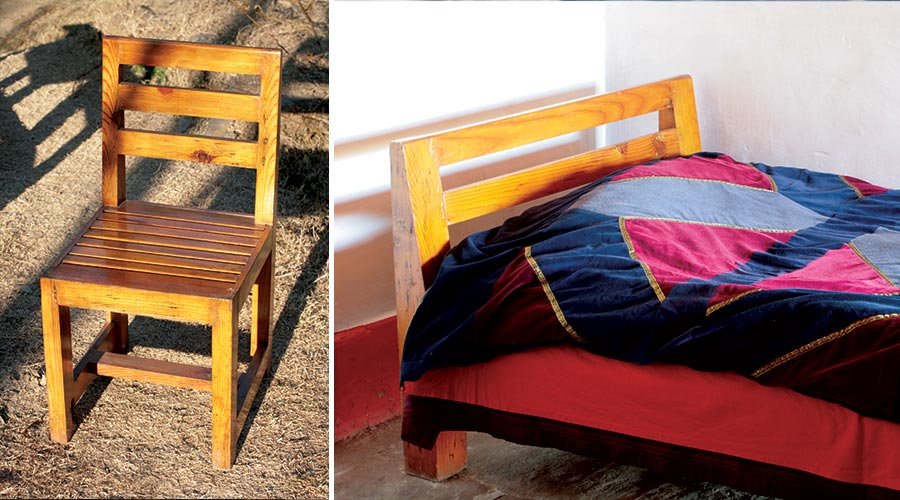
All the woodwork was done using pinewood. Sourcing legal wood when cheap illegal options were available landed us in some trouble. People thought we had lot of money to blow. This led to extortion threats from the underworld due to which our project got delayed by three months. Thankfully the issue got resolved and we were ready to sail again.
The tinned roof was laid on a solid pinewood frame. Instead of laying wooded planks over the frame, we opted for 6mm plywood. A 2 inch thick thermocol layer was sandwiched between plywood and the tin sheet. Thermocol layer helped reduce noise during rains, provided water proofing and added the much needed insulation. Wooden piping on the inner sides of the roof provide additional support to the plywood sheets while creating the visual feel similar to the roofs built with wooden planks.
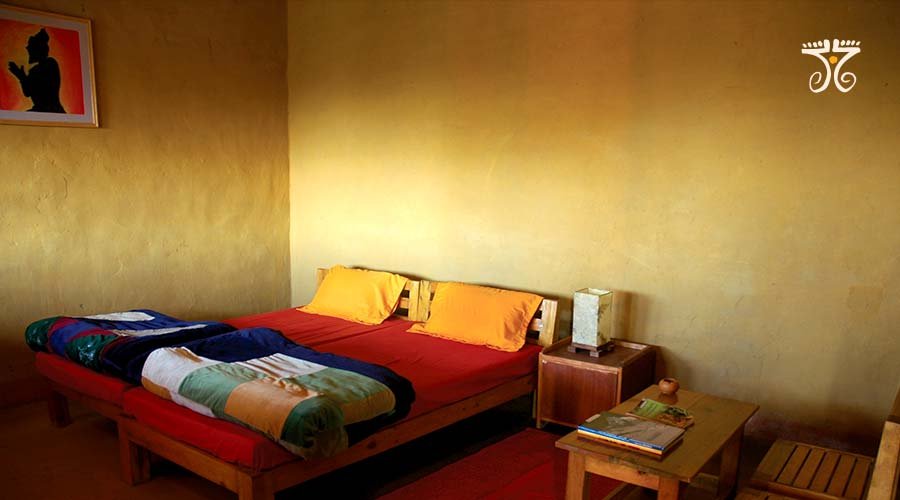
For furnishings we sourced export surplus cloth, for utensils we combed the gulley’s of old Delhi and reached Khurja for lead free ceramic ware. One even burnt midnight oil to oil paint canvases for decorating the walls of our cottages. It was fun shaping the dream.
The construction activity went on for almost 18 months. We handled the liquidity crisis through purchase of raw material on credit and short term loans from ‘friends & family’ bank. The project took off with a bang. The memories of our first trial run with a group of friends and the first formal guests, Sangita Ghaley and her colleagues, still gives me goosebumps. I cannot forget that night when the hudka beats and soulful voices of local artists filled the air while we eagerly waited for that first dinner to get over, without a glitch.
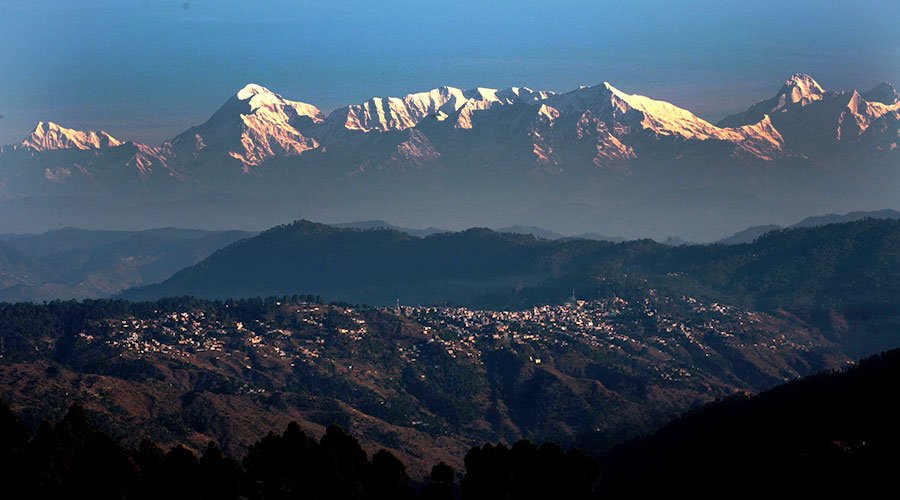
Some old friends and associations helped us a lot during these early days, especially Santhosh Babu of Training Alternatives, now ODA. The training of our staff facilitated by Rajesh Ojha of Banjara Camps and his detailed inputs on guest gastronomy helped us quickly build a brand. Thanks to friends and well-wishers like them, we managed to clear all our debts within 1.5 years and recovered investments well within three years.
Now Himalayan Village Sonapani is in the hands of friend and schoolmate Girish Melkani, who has been an integral part of the venture. He boarded the train when we were facing rough weather. But for him, Sonapani would have been a disaster at kickoff. I wish him well for carrying forward the legacy which we build together. I hope Himalayan Village Sonapani always lives up to its name!
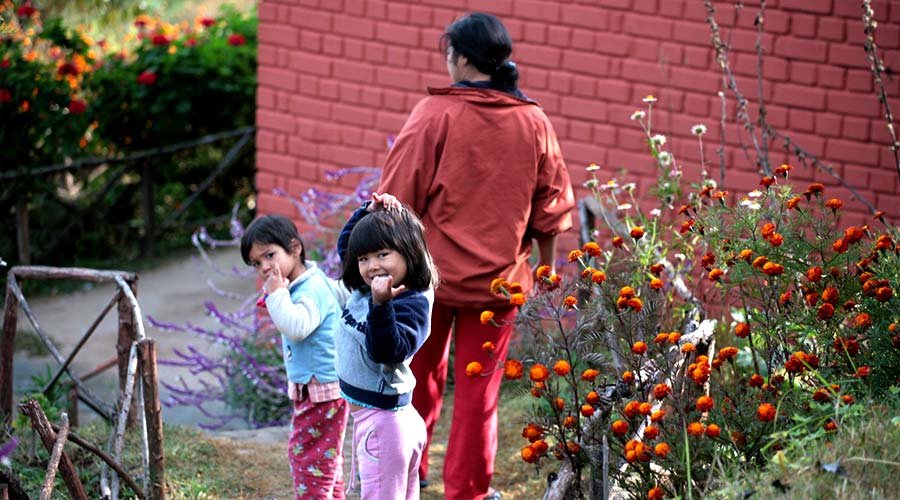
As for me, it was dream project. A dream I would cherish for long.
A dream worth living again!
Wow, a great journey for you. A lot of insights on how to develop a sustainable business in an eco-friendly way. Thanks
Fantastic insights Pangti. Sonapani is clearly a labour of love and it shows in every nuance there. Kudos to you guys for making it happen